¿Qué son?
Los robots Delta son un tipo de robot paralelo, el cual está formado por un conjunto de bielas; cada una de ellas dispone de un sistema de actuación independiente que suele estar conformado por un servomotor y un reductor. El efector final está unido a una plataforma móvil por, al menos, dos bielas; esto permite que los robots Deltas canalicen mejor la energía de los servomotores con el fin de lograr mayor velocidad en los movimientos e incrementar la capacidad de carga del efector. Dicho de otra forma, un robot Delta consta de una base fija conectada a una plataforma móvil mediante extremidades.
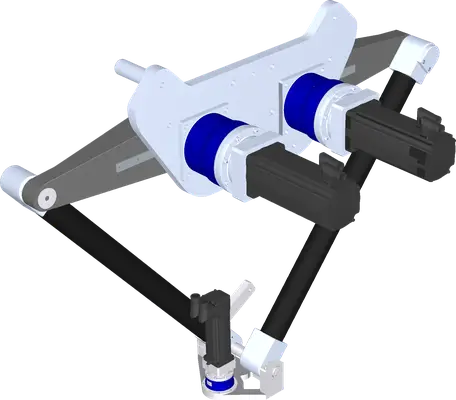
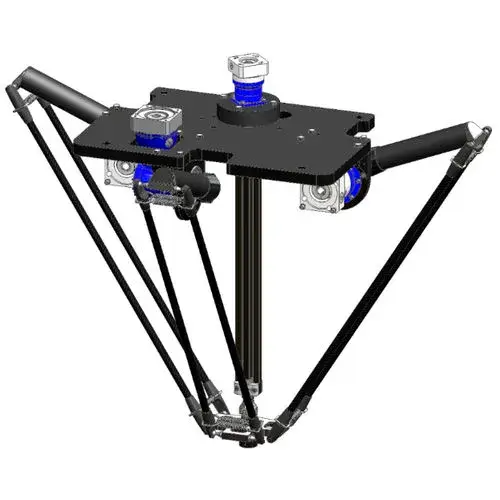
- Los robots Delta más actuales pueden llegar a disponer de hasta cinco grados de libertad y tener hasta 6 ejes.
- La base y el efector final se encuentran unidos por bielas o cadenas cinemáticas cuyo principio está basado en la aplicación de paralelogramos.
- Estos robots, en general, pueden ejecutar hasta 300 movimientos por minuto.
En este blog te presentaremos diversos detalles acerca de los robots Delta con el fin de que conozcas no solo su funcionamiento básico, sino los orígenes que respaldan su eficiencia actual y los motivos por los cuales el mercado de estos robots ha ido en crecimiento durante las últimas décadas. En la actualidad, los robots Delta son usados ampliamente para aplicaciones que llevan a cabo tareas de pick and place.
¿Cómo funcionan?
Los Robots Delta tienen la capacidad de suministrar la velocidad y aceleración requeridas sobre el efector final mediante un sistema de brazos, los cuales sirven de interfaz entre la plataforma móvil y una plataforma fija llamada base. Este tipo de construcción proporciona mayor rigidez y repetibilidad al robot.
De acuerdo con la comparación anterior, es posible entrever que el uso de ambos brazos brinda más capacidad de carga y mayor precisión. Por consiguiente, los 3 brazos (bielas o cadenas) unen la plataforma móvil a la base y permiten balancear el centro de masa de cada una de ellas gracias a que funcionan conforme a un mecanismo de paralelogramo. Dentro de esta configuración, los brazos están unidos a la base fija mediante pares o juntas universales. El diseño de los robots paralelos incluye una pierna central tipo cardán para proveer el movimiento de rotación generado desde el motor, en la base, y transmitirlo hasta la plataforma móvil.
Según lo explicado, por tanto, la composición de los robots Delta consiste en los siguientes puntos:
- El cuerpo o base que integra todas las articulaciones principales, los servomotores, los reductores planetarios y la electrónica. Particularmente, Wittenstein es la marca empleada por excelencia en los ejes de los robots Delta. Puedes conocer las alternativas para reductores de esta marca en nuestro catálogo de stock.
- Los brazos mecánicos que actúan como bielas y se encargan de desplazar el efector final sobre la superficie, siempre de forma paralela.
- El efector final en el extremo de los brazos.
- Los gripper o pinzas de vacío ubicados en el efector final, según la aplicación, los cuales realizan las tareas de recolección.
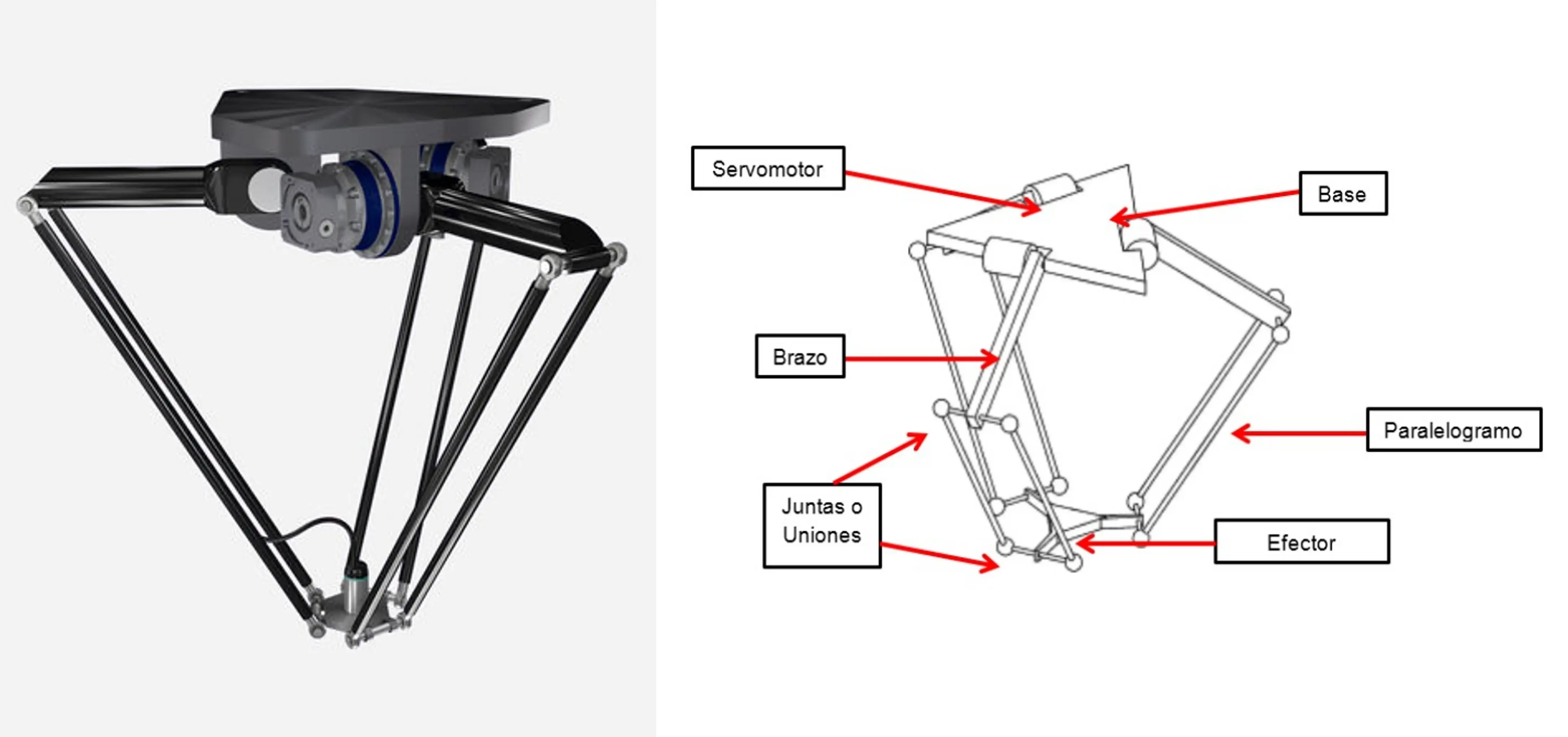
Partes de un robot Delta.
Es importante considerar que, los robots Delta operan en células o líneas de producción, por lo que, entre sus componentes deben contemplarse bandas transportadoras o sistemas que se encarguen de alimentar el material que el robot debe manipular.
¿Cuándo fueron creados?
Sin duda, la aproximación más rápida al funcionamiento de los robots Delta revelará fundamentos sobre geometría, concretamente, poliedros y sus aplicaciones. No obstante, en este blog apenas mencionaremos los antecedentes más inmediatos del siglo XX con el fin de convencerte de la valía de estos robots para las industrias actuales, según los intereses iniciales conforme a los cuales fueron propuestos, construidos y patentados.
- En la primera mitad del siglo XX, James E. Gwinnett diseñó una plataforma de simulación de vuelo para un teatro que quería ofrecer mejores experiencias de los espectáculos en escena. No obstante, este sistema patentado en 1931 nunca fue construido.
- En 1940, Willard Pollard presentó un modelo de robot con 5 grados de libertad y destinado a operaciones de pintura con espray. El diseño consistía en tres brazos de dos eslabones cada uno; los eslabones estaban unidos mediante articulaciones universales. Los tres actuadores de la base comandaban la posición del herramental; al mismo tiempo, la orientación era proporcionada por otros dos actuadores colocados en la base y que transmitían el movimiento al herramental mediante la rotación proporcional de cables flexibles.
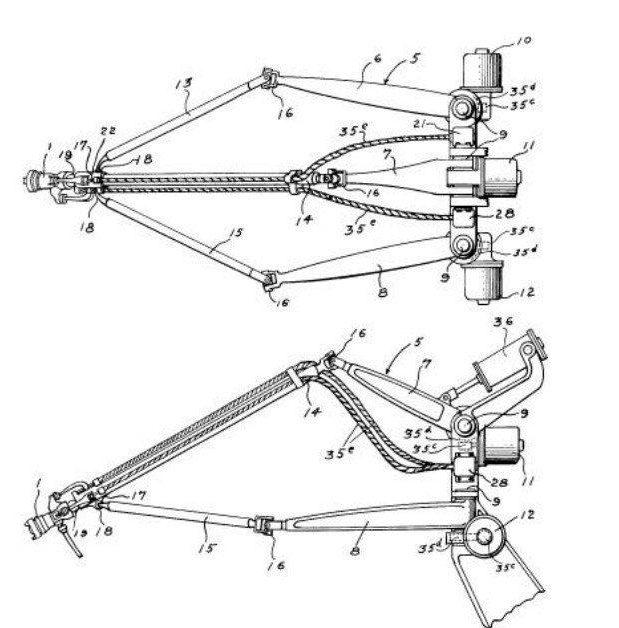
- En 1947 el doctor Eric Gough diseñó una plataforma tipo hexápodo con forma de octaedro y con lados de longitud variable; esta tenía como finalidad analizar el comportamiento de los neumáticos fabricados por Dunlop bajo cargas aplicadas en diferentes ejes. En otras palabras, buscaba simular el proceso de aterrizaje de un avión para resolver problemas asociados con las cargas.
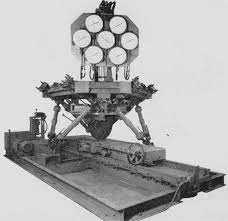
- En 1965, D. Stewart presentó un artículo en el que describía una plataforma de movimiento con 6 grados de libertad y destinada a trabajar como simulador de vuelo. Por su parte, Klaus Cappel patentó en 1967 un simulador de movimiento basado en un hexápodo. Ambos antecedentes dan lugar a la aportación de K. H. Hunt, quien sugirió en 1978 que los mecanismos paralelos empleados para los simuladores de vuelo se usaran como robots manipuladores; además, insistió en estudiar con mayor profundidad el potencial de los manipuladores paralelos para las aplicaciones robóticas con el fin de emplear sus ventajas en cuanto a rigidez y precisión.
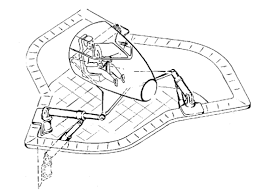
- En 1979 McCallion y Pham propusieron por primera vez utilizar la plataforma diseñada por Stewart como un manipulador paralelo para una célula de ensamblaje robotizada. Esta idea les surgió, principalmente, porque la posición del efector final es mucho menos sensible a los errores en comparación con los sensores ubicados en las articulaciones de los robots en serie. Dentro de este sistema paralelo, la rigidez garantiza que las deformaciones de los actuadores sean mínimas y contribuye, de esta manera, a lograr mayor precisión en el posicionamiento del manipulador.
Sin perder de vista los antecedentes mencionados, la invención del robot Delta actual corresponde a Reymond Clavel y es fechada en 1985, año en que le fue otorgada la patente. Clavel consolidó la idea de utilizar paralelogramos para construir una estructura robusta con tres grados de libertad de traslación y un movimiento rotatorio. A esta estructura se le dio el nombre de robot Delta.
La idea concreta del diseño de los robots Delta es el uso de paralelogramos utilizados para que un eslabón de salida tenga una orientación fija con respecto a un eslabón de entrada. Al usar tres paralelogramos, la orientación de la plataforma móvil queda totalmente restringida; esto hace que dicha plataforma se traslade únicamente sobre los tres ejes del plano cartesiano.
Actualmente, la EPFL (Escuela Politécnica Federal de Lausana, ubicada en Suiza) afirma que existen cerca de 10 000 unidades de estos robots que están operando en todo el mundo, principalmente, en el sector del embalaje. Entre las últimas innovaciones de este tipo de robots, se encuentra el Delta Direct Drive, desarrollado en colaboración con Bosch y presentado en Dusseldorf, Alemania en el 2011. Este diseño se destaca porque consigue aceleraciones por encima de los 15 segundos.
¿Por qué son la mejor alternativa para la industria del embalaje?
Si te dedicas a la industria del embalaje o requieres garantizar la calidad de tu producto mediante una manipulación automatizada de este, los robots Delta se posicionan como la solución estándar y de gran eficiencia para ello. Esto se debe, en gran medida, al origen conforme al cual Clavel consolidó el diseño y funcionamiento de este tipo de robots hasta patentarlo.
Reymond Clavel realizó sus estudios en la EPFL y obtuvo el grado de ingeniero mecánico en 1973. El ámbito al que se dedicó durante 9 años fue el de la fabricación de máquinas de escribir para Hermes Precisa International. Con su especial interés en la automatización de procesos y su experiencia en el ámbito de la fabricación, regresó como profesor al EPFL para enseñar robótica y microingeniería; este fue el nicho que le permitió concebir la idea para construir un robot de alta velocidad. Dicho robot tenía el propósito de funcionar para una fábrica de chocolate.
¿Por qué no desarrollar un robot que pueda colocar, automáticamente, bombones de chocolate dentro de sus paquetes?”
EPFL, Reymond Clavel, creator of the Delta Robot, reflects on his career
Con este curioso planteamiento, el equipo de laboratorio de Clavel comenzó a trabajar sobre la idea de incluir motores hidráulicos al diseño del robot para obtener mayor potencia; sin embargo, el enfoque no tardó en cambiar cuando tomaron en cuenta la ligereza de los bombones, pues cada uno de estos pesaba solamente cerca de 10 gramos. Entonces, la solución debía ser un robot con brazos ultraligeros.
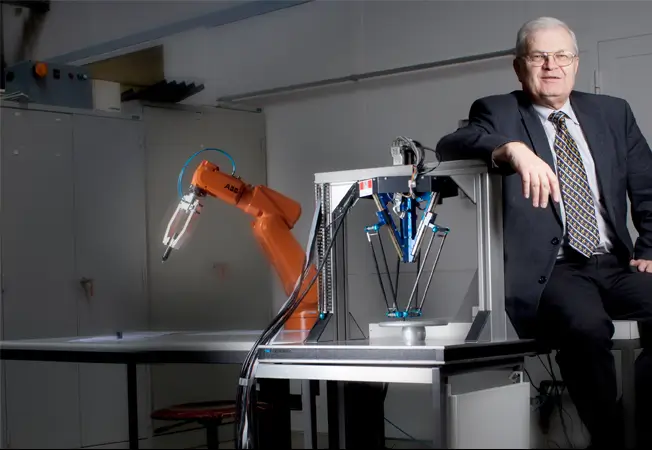
Luego de diversas pruebas y búsquedas de inspiración para dar con el diseño perfecto, Clavel determinó, junto con su equipo de laboratorio, que el robot tendría que estar compuesto por 3 brazos articulados que guiaran el dispositivo de agarre a través de tres grados de libertad en traslación. En cuanto a los componentes más pesados del motor, estos debían ser colocados en la base del robot y no en la parte móvil. Gracias a esto, los robots Delta siempre se han destacado por ser ligeros y rápidos; por ello, han ido ganando cada vez más terreno en el sector de la fabricación.
Razones para incluirlos en tus líneas de producción
Como puedes ver, los fundamentos de la invención del robot Delta hacen que destaque por su excelente relación de carga admisible-peso propio. Dado que los accionamientos de potencia conectan directamente la base del robot al efector final, dichos accionamientos sirven como elementos estructurales y actúan de forma simultánea; esto les da la capacidad de manipular cargas muy superiores a su propio peso. En resumen, la elevada proporción carga-potencia de estos sistemas brinda una alta eficiencia energética.
Alta rigidez y muy bajo peso, el resultado es una precisión superior a la de los robots en serie.
El diseño innovador, pues, de los robots Delta consiste en que emplea los actuadores en la base, por lo que, las barras en movimiento requieren menos masa e inercia para soportar las cargas. Gracias a esta configuración, el robot puede lograr aceleraciones de 50 G en entornos experimentales y de 12 G en aplicaciones industriales.
En general, estos tipos de robots son ideales para transportar objetos de bajo peso (de 10 g a 1 kg) y, con ello, son excelentes alternativas para la industria de ensamble, alimenticia o empaque.
Con base en todo lo anterior, solo queda afirmar que los robots Delta proporcionan a las líneas de producción las siguientes ventajas:
- Productividad: alcanzan tasas de productividad mucho más elevadas gracias a su velocidad y rendimiento. Pueden procesar hasta 3 objetos por segundo o 200 objetos por minuto, lo que aumenta significativamente el rendimiento.
- Seguridad: al tener la capacidad de realizar procesos a altas velocidades y gran repetibilidad, evitan a los operarios humanos lesiones por estrés y fatiga. Por lo mismo, estos robots contribuyen a reducir la insatisfacción laboral.
- Espacio: suelen ser montados en el techo, lo que los hace ideales para ahorrar espacio y sumarse a una celda de trabajo robótica ya integrada.
Por último, los robots Delta están diseñados, especialmente, para aplicaciones de baja carga útil tales como actividades de ensamblado o pick and place. Por lo mismo, son complementos perfectos para la industria alimentaria, electrónica, cosmética y farmacéutica. Además, con el paso del tiempo, las mejoras realizadas a los robots Delta hacen que estos ya no se limiten solo a tareas de embalaje y ensamblaje, sino que sean empleados para aplicaciones de ultraprecisión (en escala de nanómetros), cirugía robótica remota, relojería y mecanizado de precisión; asimismo, pueden desempeñarse para simuladores de vuelo, manipuladores de grandes cargas y posicionamiento de antenas.
Ahora que ya conoces el qué, cómo, cuándo y por qué de los robots Delta, te invitamos a revisar las alternativas disponibles para ti gracias a nuestra colaboración con Weiss, empresa alemana líder en la fabricación de indexadores mecánicos y de soluciones innovadoras como el DR Delta Robots.
En URANY tenemos disponibles soluciones versátiles para la manipulación eficiente de mercancía o piezas de producción. ¡Contáctanos para recibir una asesoría técnica gratuita y conocer las mejores soluciones!
¡Evoluciona tus procesos de montaje con URANY!